|
|
|
INTERNATIONAL COMPARISON OF
THE HOURLY LABOR COST
IN THE PRIMARY TEXTILE INDUSTRY
2007
The average labor costs shown
in this report, might not always check with the official statistics of the
respective countries for the textile industry. They are based on data collected
and made available to Werner International and are a realistic representation of
the actual labor costs. This service Werner International provides to its
clients since 1968 and is based on data supplied by a panel of Werner clients in
each of the participating countries.
GENERAL OBSERVATIONS
The global competitive landscape in textiles and clothing has undergone a major
shift with the implementation of WTO agreements on textiles & clothing in 2005
and the introduction, since then, of a large number of regional trade
agreements.
Within this post-MFA era characterized by open competition, all successful
volume strategies are fundamentally driven by cost leadership. Cost advantages
can be achieved in manufacturing through effective global sourcing and by taking
advantage of the considerable wave of new investments in the Industry.
What appears clear is that competitiveness in the textile industry is affected
by many external and internal factors and that most low-cost, developing
countries are now under heavy competitive pressure from the two textile and
apparel giants: China and India which continue to gain market share thanks to
their unique scale and scope. The rapid commoditization of the lower segments of
the global market and the strong price competition, which this situation has
fuelled, are indeed already eroding the positioning of many companies and
countries.
It is within this perspective that the new labor cost comparison has to be seen.
The Werner International 2007 Labor Cost Comparison in the primary textile
industry is the first study comparing the hourly labor cost in 44 countries
since the phasing out of the MFA agreement. We believe that this study fairly
represents the situation for the vast majority of textile producers in the
world.
As we already did for previous editions, we would like to stress that the hourly
labor cost is but one of the many factors which impact the competitiveness of
the textile industry.
A factor for labor productivity has to be introduced in each case to arrive at a
more meaningful unit labor cost. But even then, it can only give a limited view
of the total competitiveness of the primary textile industry since total
competitiveness depends on a wide range of other cost and non cost, external or
internal factors such as exchange rates, raw material and energy costs, interest
costs, inventory turnover, throughput time, quality, value adding capabilities,
etc.
Werner Labor Cost Comparison covers all primary textile industry sectors,
consisting of spinning, weaving and dyeing & finishing. Cut & sewing operations
are not part of these comparisons. Labor cost in the clothing industry is in
fact much more difficult to compare since the industry is highly fragmented,
with large fluctuations within same geographical regions and size of company. In
many countries the informal sector is still occupying a significant position.
At Werner we are particularly proud to once again offer this survey to the
global industry, fully aware that labor cost remains a dominant factor in
driving the relocation dynamics of this Industry.
We are also pleased to see the overall rise of labor costs across all developing
countries, proof of the capability of this industry, within the globalization
revolution, to act as a strong wealth distributor playing a fundamental role in
the development path of developing countries.
Constantine Raptis
President
COMMENTS
Switzerland is still in first place with the highest hourly labor cost in
the textile industry, a position it has held almost continuously since 1987.
Amongst the top ten most expensive labor cost countries, European Union
countries take seven positions, with only Spain, Greece and Portugal having a
somewhat lower hourly cost. Japan has dropped from the first place in
2000 to the sixth place in 2007. Several of the positions have changed, most of
this is due to changes in the exchange rate to the United States Dollar. The USA
itself is occupying the 11th place. While in 2000 the USA ranked higher
than Italy, France and the UK, the actual strong Euro has altered the
classification.
There is not much movement in the lower part of the ranking: the lowest labor
costs are noted in Asia, with Bangladesh, Pakistan, Vietnam, China Inland and
Indonesia. Remarkably however is the continuous increase in labor costs in
the coastal region of China, approaching rapidly the one dollar per
operator hour threshold.
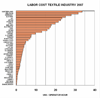
Labor cost textile industry 2007
Within Eastern Europe,
overall labor cost has been catching up fast, with most countries now between 3
and 5 US$ per hour. Only Bulgaria and Romania have substantially lower labor
costs, these are however forecasted to increase substantially with the entry
into the European Union.
Hong Kong, S-Korea and Taiwan are between 15th and 20th position with
around 7 US$ per operator hour.
The effect of rising labor costs in Eastern Europe as a consequence of joining
the European Union is obvious: since 2002, the cost in local currency increased
almost 30%, while in Western Europe this was not even 13%. The following graph
is showing the increase in labor cost in the textile industry since 2002, by
region in the world, in local currency and US$.
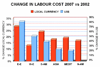
Change in labour cost 2007 vs 2002
Latin American countries
have seen the second highest increases in cost since 2002 measured in local
currency. In US$ terms, they are at about the same level as many Mediterranean
countries (Turkey, Morocco, Tunisia) and S-Africa.
It should also be noted that in some countries, there is a substantial
difference in hourly labor cost from company to company, from region to region,
from spinning to finishing, from large to smaller company, etc.
As in the past, the variation in exchange rate of U.S. dollar is having a bigger
impact, in many cases, than the actual increases in local currency.
If you would like to receive a full copy of the new Wage Report,
please request your full LCC report by email. We will e-mail you the Wage Report within 24 hours.
CLICK below to :
-
Request full LCC report in ENGLISH
-
Request full LCC report in TURKISH
-
Request full LCC report in RUSSIAN
Back to top
|
|
 |
|
|
APTMA APPOINTS WERNER TO
CONDUCT EXTENSIVE PERFORMANCE EVALUATION OF PRIMARY PAKISTAN TEXTILE MILLS |
|
|
|
| |
APTMA APPOINTS WERNER TO CONDUCT EXTENSIVE PERFORMANCE EVALUATION OF PRIMARY
PAKISTAN TEXTILE MILLS
Pakistan is the fifth largest
producer of cotton in the world, the third largest exporter of raw cotton, the
fourth largest consumer of cotton, and the largest exporter of cotton yarn. 1.3
million farmers (out of a total of 5 million) cultivate cotton over 15 per cent
of the cultivable area in the country. Cotton and cotton products contribute
about 10 per cent to GDP and 55 per cent to the foreign exchange earnings of the
country.
Taken as a whole, between 30 and 40 per cent of the cotton ends up as domestic
consumption of final products. The remaining is exported as raw cotton, yarn,
cloth, and garments. Cotton production supports Pakistan’s largest industrial
sector, comprising some 400 textile mills, 7 million spindles, 27,000 looms in
the mill sector (including 15,000 shuttleless looms), over 250,000 looms in the
non-mill sector, 700 knitwear units, 4,000 garment units (with 200,000 sewing
machines), 650 dyeing and finishing units.
Textiles is the premier industry & backbone of Pakistan’s Economy as it
generates more than 65 % of exports. The textile and apparel industry in
Pakistan constitutes 46 % of Manufacturing Industry and employs almost 40 % of
country’s working population. Over USD 4 billion of textile and garment
machinery has been imported in Pakistan in the last few years that has
significantly improved the quality and productivity of the Pakistan textile and
apparel sectors.
In order to contribute and support the competitiveness of its textile and
garment industry in the now globalized marketplace, the APTMA (All Pakistan
Textile Mills Association) and the Ministry of Textiles have requested Werner
International to conduct a thoroughly investigation and assessment exercise on
the actual performance of a selected number of textile and clothing companies
across the country.
The World Textile and Apparel industry is undergoing a tremendous era of changes
characterized by the rapid relocation of the majority of productions out of
western countries and the increasing level of competition among new supplying
countries with China and India expected to rapidly gain hegemony over global
textile and apparel trade. While capacity build-up in anticipation of quota
removal has created the optimal conditions for large Western buyers and
retailers to exercise their increased negotiating power, commodities prices are
reaching for unheard lows. In this context national governments of new leading
textile countries are constantly intervening playing a relevant role in
determining the overall competitiveness of their commodity textile
industry. Within this context this initiative’s objective is twofold. On one
side assess and evaluate the level of internal competitiveness of participating
companies through the execution of an deep and detailed analysis and auditing.
On the other provide companies with e benchmarking comparison of their
performance to those achieved by best similar competitors all over the world and
therefore specifically outline gaps and improvements potentials.
In order to effectively compete in the challenging global stage, both textile
leaders and policy makers must fully grasp the challenges and opportunity of
this new era in order to successfully develop coherent strategies at both
company and sector level. Awareness about its current strengths and
weaknesses and visibility over global best practices no doubt represent the
necessary platform for proper strategy and policy making. Werner International
is honored to have provided his assistance in the execution of this
comprehensive exercise including on site audits, management workshops and data
analysis and benchmarking.
At Werner International we felt uniquely qualified to carry out this project,
having provided management and strategic consulting services exclusively to
fiber, textile and fashion clients on a global basis for over 60 years. We are
confident and committed to make this important initiative into the first step of
a long term collaboration with the Pakistani government and entrepreneurs
with the shared goal to contribute to the future success of their textile
industry in the global market.
Back to top
|
|

NATHAN AND WERNER INTERNATIONAL IN THE DOMINICANS:
NEW APPAREL
PREPRODUCTION CENTER TO TRAIN APPAREL WORKERS
 |
|
|
|
|
|
|
|
|
NEW
CENTER OFFERS DOMINICAN APPAREL WORKERS PREPRODUCTION TRAINING
In a new garment preproduction
training center in the Santiago Industrial Free Zone, 12 Dominican apparel
workers have learned how to design patterns and make samples and markers so the
firms they work for can meet heightened competition. Another 50 workers will be
trained by the end of 2006.
Textile and apparel exports make up more than a third of the Dominican
Republic’s exports and are the source of livelihood for many Dominicans. But
when U.S. and European textile import quotas were lifted in 2005, apparel
exporters from Asia began competing directly with exporters that had benefited
from the quota system. Deep reductions in textile exports from the Dominican
Republic’s free zones are likely if the country’s textile and apparel industry
does not change tactics and find new market niches.
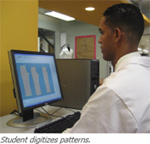
In the post-quota environment, the
Dominican Republic’s simple cut and sew operations will find it difficult to
compete by reducing costs alone. The alternative is to increase product value by
offering the preproduction services that many apparel buyers demand. A full
range of preproduction services includes sourcing fabric and trim and developing
patterns, samples, and markers.
Recognizing that few small and
medium-sized Dominican producers are in a position to provide such value-added
services, USAID helped fund a center to train apparel industry employees in
preproduction. To establish the center, Nathan Associates and partner Werner
International formed a partnership with two Dominican industry groups and a
government–supported technical
training institute.
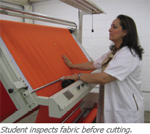
Nathan, with its partner Werner
International, designed the center, selected the building site, and oversaw
construction of the additions; trained instructors and facility supervisors in
preproduction skills such as design, pattern and marker making, and cutting; and
prepared training materials and documentation on the proper use of equipment.
Dominican partners provided
the land, equipment, supplies, operating expenses, and personnel.
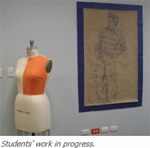
The skills taught in the Santiago Training Center will enable the Dominican
apparel industry—so vital to the country’s economy—not only to retain clients
but penetrate new markets and acquire new clients as well.
Back to top
|
|
ADVANCED ORGANIZATIONAL APPROACHES IN FASHION PRODUCTION: CELLULAR MANUFACTURING
Werner International is currently
pioneering in the application of advanced organizational models in apparel and
fashion production.
We are all aware of the fact that competition in the fashion retail industry
will increasingly be played on the capability to align marketing effectiveness
and supply chain rationalization - manufacturing optimization. Volumes
fragmentation and shorter lead times appear today as the key competition factors
in the medium to high market segments.
The rapid evolution of market conditions are exposing the limits of traditional
manufacturing models in their capability to respond to these new challenges
which require the capability to reduce value-less complexity while developing
more responsive manufacturing approaches.
Today the shift from traditional, rigid line/section apparel
manufacturing to cellular is a must in all these countries where large
volumes of standard items are not produced anymore because of the relatively
high local labor cost. The strategic role of such manufacturing locations can
only be that of flexible and responsive proximity suppliers. Complexity becomes
the rule, creating the necessity for a strong effort in rationalization and
management of complexity to preserve profitability.
The reduction of complexity in the design of ranges in the fashion industry can
be achieved on one side by rationalizing the architecture of the range
and on the other by “rationalizing” the product complexity and their
“manufacturing flow”.
Generally, we are assisting to a relevant effort to expand the culture of
production “postponement”, this to take better advantage of the now available
continue flow of sell-out information and by the parallel development of
industrial logics focused on the segmentation of products into “modules”.
The objective is to identify the commonalities of parts and components
and in the search for differentiation activities in the latest possible stages
of the production cycles. This to preserve and improve offerings’ depth,
attractiveness and freshness, while at the same time compressing variety and
therefore complexity which does not create value added for the consumer.
Apparel Cellular Manufacturing is a production system achieved with a specific
layout which provides a much higher volume flexibility and the parallel
improvement of a number of operational parameters such as those related to
production buffers and work in process.
Apparel Cellular Manufacturing is obtained by re-engineering the layout (Cell
Design) and the production system by creating “production islands” with the
objective of streamlining and shortening the gaps between the different
production phases. Cellular Manufacturing is a hybrid production system between
the classic production by departments (every phase is carried out by a different
departments and executed by lot) and the production line (lines of operators
where each highly specialized operator carries out a small phase of the
production cycle and where the single product is moved by conveyer belt).
This system provides a much higher degree of flexibility compared to the
traditional line set-up (which is balanced by dividing the production cycle in
elementary phases) and a shorter overall lead time in respect to the classic
production by lots (by reducing the time of lot making-up and the time of
product movements)
The guiding idea of this approach is the “transparency” of the process: the
objective should be the creation of a “Visual Factory”, which is
highly intuitive and where problems, deviations, abnormalities, waste can be
easily spotted. The layout engineering should foster interpersonal
communications as well as the use of visual signaling systems. Furthermore, all
production support tolls need to have a clear location so that their status can
be immediately identified.
Layouts need to be flexible so that new products, unforeseen volumes, new
materials, new processes and new technologies can be quickly implemented. The
key objective is in fact to allow a virtually constant process reallocation.
In other words, the modification of a production line flows or the introduction
of a new machine or technology should not be a lengthy and costly process.
The main characteristic of each cell must be its flexibility to mix and volumes
dynamics, this obtained without compromising efficiency.
Cell Design therefore means engineering layouts that allow to rapidly:
-
adjust the number of cell
workers when the product volume changes with minor impacts on both the
efficiency and effectiveness of the company
-
Change productions without
high set-up times
-
Minimize transportation costs
(and its indirect costs) within a cell
-
Minimize inactive time of the
operators
KEY
OBJECTIVES OF FASHION CELLAR MANUFACTURING |
OBJECTIVES
AND ADVANTAGES
|
KEY SUCCESS
FACTORS |
Greatly improve versatility and
responsiveness to market requirements in terms of timing, quality,
volumes and service |
Requires strong focus on training of
personnel across all processes and work cycles |
Leverages
on the greater autonomy given to employees: Human Capital |
Slim and
simplify control systems |
Requires
strong analysis of Company specific product ranges structures and work
cycles: there is no standard cell manufacturing |
Provides
better visibility over targets to wider audience in the organization |
Reduce
capital investment in intermediate stocks, buffers and work in progress |
“internal
marketing”: need to build a comprehensive modern manufacturing culture
|
A recent study on a sample of
companies which have migrated to a cellular manufacturing organization has tried
to outline the following benefits:
|
Average
|
Quality
improvement |
65% |
Reduction of
labor cost on total direct costs |
3% |
Labor Efficiency
improvement |
10% |
Reduction of
time spent in not value added generating activities |
40% |
Reduction of %
of indirect vs. direct labor (less supervisors and controllers) |
10% |
Reduction of
necessary work space (less stocks and buffers) |
37% |
Reduction of
absenteeism |
40% |
Reduction in
stocks – buffers – work in progress |
70% |
Responsiveness
–Reduction of throughout time |
80% |
Back to top
|
| |